The filter media of our filter program consist either of specially treated papers, non-woven materials or multilayer filter media, depending on specifications and applications.
Filters made from paper
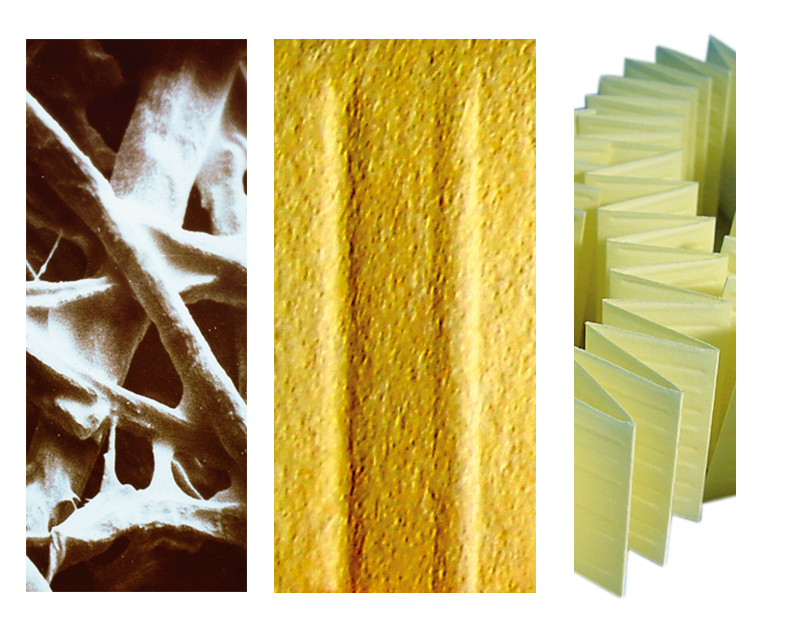
The paper for our filters is made from high-grade cellulose fibers impregnated with special resins. These materials are treated in a special production process: special pre-warming prepares the paper for the embossing of vertical ridges. Afterwards, the paper is folded according to requirements. Then the impregnation is cured to make the paper mechanically stable and to make it resistant to chemical and thermal influences. The result: filters with stable pleat geometry that prevent the feared forming of blocks under high load and ensure that air, oil or fuel can flow freely through the paper at all times. The filters can remove particles as small as 1 micron, depending on the requirements, and offer safe conditions for highest contaminant elimination.
Filters made from paper are used in air, fuel, oil and hydraulic filters.
Block forming in air filters - an expensive phenomenon
When the pleat geometry is unstable and the folds are too close together, little or no air can flow through the filter in these areas. This increases flow resistance, filtration deteriorates, the service life of the filter is reduced and fuel consumption and pollutant emissions increase significantly.
In order to prevent loss of stability and shape, our filter paper is impregnated with special resins during a complex treatment process.
Filter non-woven materials
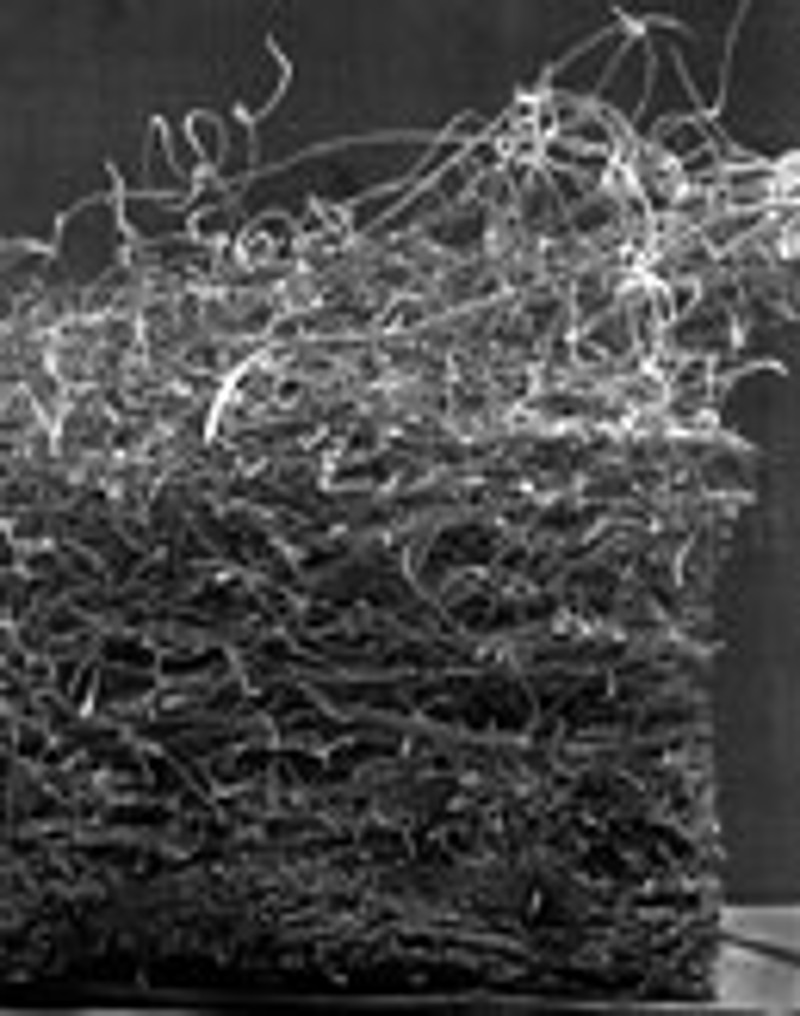
Non-woven materials, on the other hand, consist of plastic fibers with thicknesses in the micron range: the finer the fibers, the better the separation. The non-woven materials are applied in layers in which the density and fineness of the fibers increase from the dirt side to the clean side. This so-called funnel effect allows efficiencies of up to 99.9 percent with low flow resistance at the same time.
For some years now fleece has been used for cabin filters as well as for new developments in the oil filter sector. Recently, fleece is also increasingly being used in air filters – with the advantage of up to 40 percent increase in filter performance and a longer service life. Fleece is also being used increasingly in fuel filters, mostly combined with stabilizing base paper.
Multilayer filter media
These are combinations of non-woven materials and paper that have been fused in a complex production process. Compared to conventional paper filters, these filters eliminate up to 40 percent more contaminants, with particle sizes as small as 3 to 5 microns.
Multilayer filter media are used for modern diesel fuel injection systems (in turbo diesel direct injection, common rail or pump injector technology).
One of the most important requirements for optimum engine performance, high torques, low fuel consumption and minimized pollutant emission: clean intake air. This, however, depends very much on the air filter, which has to prevent dust, soot and tire wear particles from entering the intake system.
THE ESSENCE OF A GOOD AIR FILTER
An important quality characteristic is the so-called collection efficiency. It is measured in percentage and indicates the proportion of particles from the intake air that remains in the filter. MAHLE air filters achieve here up to 99.9%. This means that practically everything that can affect the function and service life of the engine is filtered out by them – and this creates the conditions for long engine service life even under-extreme temperatures or chemical effects.
FOR INCREASED ROAD SAFETY: THE FLAME-RETARDANT DESIGN
In order to prevent engine compartment fires, the car manufacturers have taken special design measures. These include grids in front of the air intake opening or suitable positioning of the air intake duct. Another option for fire prevention is the design of filter elements with flame retardant properties such as those developed by MAHLE in cooperation with car manufacturers and paper makers. Such filter media with flame retardant properties are mandatory in the specification books of car manufacturers for future vehicle generations.
THE THREEFOLD SAFE EFFECT
The basis for achieving flame retardant properties is a special resin used to impregnate the filter paper. The resin proportion for filter media with flame retardant treatment is between 25 and 30% (for normal filter paper this is only 15 to 20%). The paper treated in this way can catch fire, but extinguishes very soon afterwards. The effect is based on three fire extinguishing measures:
- Release of nitrogen (N) to smother the fire as an inert gas
- Release of water to quench the temperature to below the combustion point
- Release of acid to oxidise the cellulose fibres so that they become incombustible